Plastic extrusion for creating standardized, premium parts
Plastic extrusion for creating standardized, premium parts
Blog Article
Recognizing the Basics and Applications of Plastic Extrusion in Modern Production
In the realm of modern production, the technique of plastic extrusion plays a critical duty. Deciphering the principles of this procedure discloses the true adaptability and possibility of plastic extrusion.
The Principles of Plastic Extrusion Process
While it may show up complex, the basics of the plastic extrusion process are based on reasonably simple concepts. It is a production process where plastic is melted and after that formed right into a continual account via a die. The raw plastic material, often in the form of pellets, is fed right into an extruder. Inside the extruder, the plastic is subjected to heat and pressure, creating it to melt. The molten plastic is then forced through a shaped opening, known as a die, to form a long, continuous product. The extruded product is cooled down and after that cut to the preferred size. The plastic extrusion procedure is extensively used in different markets due to its flexibility, cost-effectiveness, and effectiveness.
Different Kinds Of Plastic Extrusion Strategies
Structure upon the standard understanding of the plastic extrusion process, it is needed to discover the various techniques entailed in this production approach. In comparison, sheet extrusion produces large, level sheets of plastic, which are generally additional refined into products such as food product packaging, shower drapes, and auto parts. Recognizing these methods is key to making use of plastic extrusion properly in modern production.
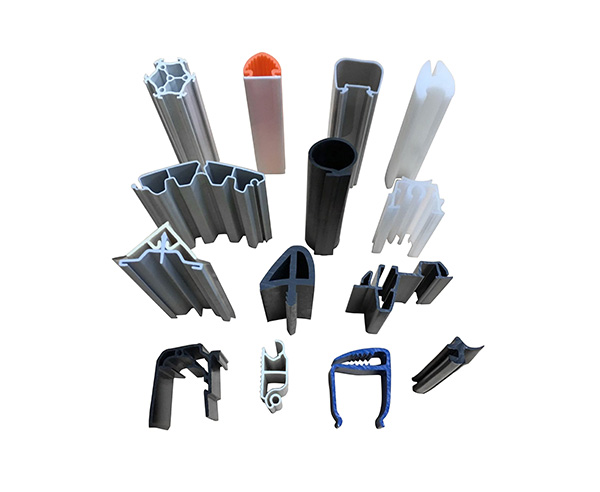
The Duty of Plastic Extrusion in the Automotive Market
A frustrating majority of parts in modern vehicles are items of the plastic extrusion process. Plastic extrusion is mostly utilized in the manufacturing of numerous vehicle elements such as bumpers, grills, door panels, and control panel trim. Thus, plastic extrusion plays a pivotal role in automobile production.
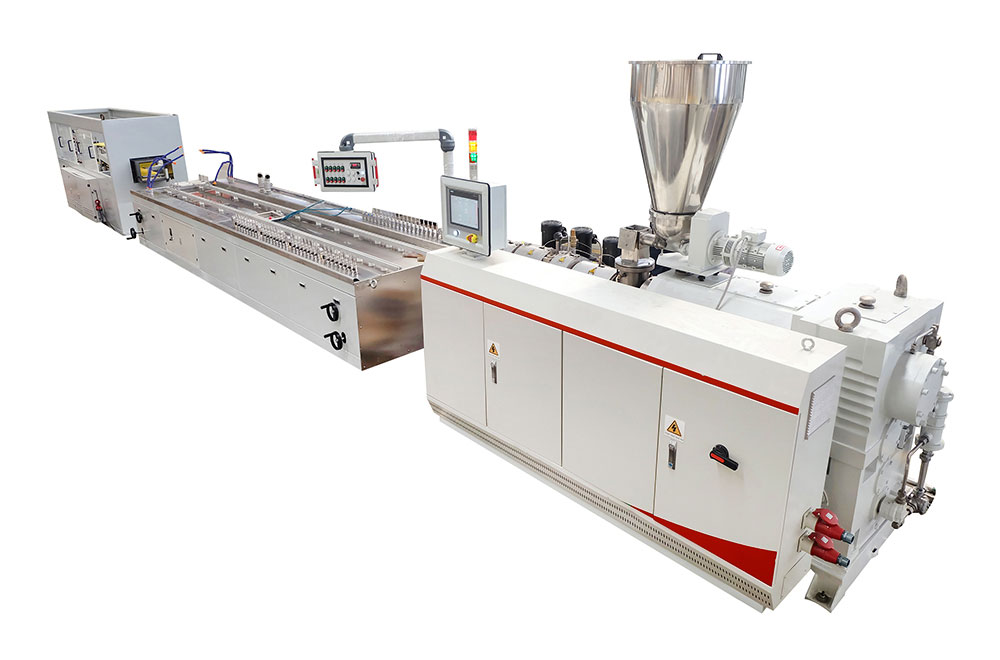
Applications of Plastic Extrusion in Durable Goods Manufacturing
Past its considerable effect on the vehicle sector, plastic extrusion shows similarly effective in the realm of customer products manufacturing. This process is vital in creating a large range of items, from food product packaging to household home appliances, playthings, and also medical devices. The flexibility of plastic extrusion permits makers to create and produce complicated sizes and shapes with high accuracy and efficiency. Due to the recyclability of several plastics, extruded Related Site components can be recycled, minimizing waste and expense (plastic extrusion). The adaptability, versatility, and cost-effectiveness of plastic extrusion make it a recommended option for my website numerous consumer goods producers, contributing dramatically to the industry's growth and advancement. However, the ecological implications of this prevalent usage need careful factor to consider, a subject to be gone over even more in the subsequent area.
Environmental Influence and Sustainability in Plastic Extrusion
The pervasive usage of plastic extrusion in manufacturing invites scrutiny of its ecological ramifications. As a process that frequently makes use of non-biodegradable products, the environmental effect can be substantial. Power usage, waste manufacturing, and carbon exhausts are all problems. Sector advancements are increasing sustainability. Effective equipment minimizes power use, while waste administration systems recycle scrap plastic, lowering raw product needs. Furthermore, the advancement of biodegradable plastics supplies an extra ecologically friendly alternative. Regardless of these improvements, better see here advancement is needed to reduce the environmental footprint of plastic extrusion. As society leans towards sustainability, producers should adapt to continue to be viable, stressing the significance of constant study and advancement in this area.
Final thought
Finally, plastic extrusion plays a crucial duty in modern manufacturing, especially in the automobile and customer items industries. Its flexibility enables the manufacturing of a wide variety of parts with high precision. Additionally, its possibility for reusing and development of eco-friendly materials supplies an encouraging avenue towards lasting techniques, therefore resolving ecological problems. Comprehending the fundamentals of this process is key to maximizing its benefits and applications.

The plastic extrusion process is extensively used in different industries due to its performance, adaptability, and cost-effectiveness.
Structure upon the fundamental understanding of the plastic extrusion procedure, it is needed to discover the various strategies included in this manufacturing technique. plastic extrusion. In comparison, sheet extrusion creates large, flat sheets of plastic, which are usually additional refined into items such as food packaging, shower drapes, and cars and truck components.A frustrating majority of parts in contemporary vehicles are items of the plastic extrusion procedure
Report this page